Een sportwagen van minder dan achthonderd kilo bouwen? Donkervoort doet het. Het geheim zit niet alleen in geavanceerde materialen zoals koolstofvezel, maar vooral in het ontwerp en de precisie van de constructie. Een cruciale rol is hierbij weggelegd voor Dumaco, dat onder meer de stalen buizen levert voor het chassis. Samen ontwikkelen de bedrijven oplossingen om tot op de millimeter nauwkeurig te werken.
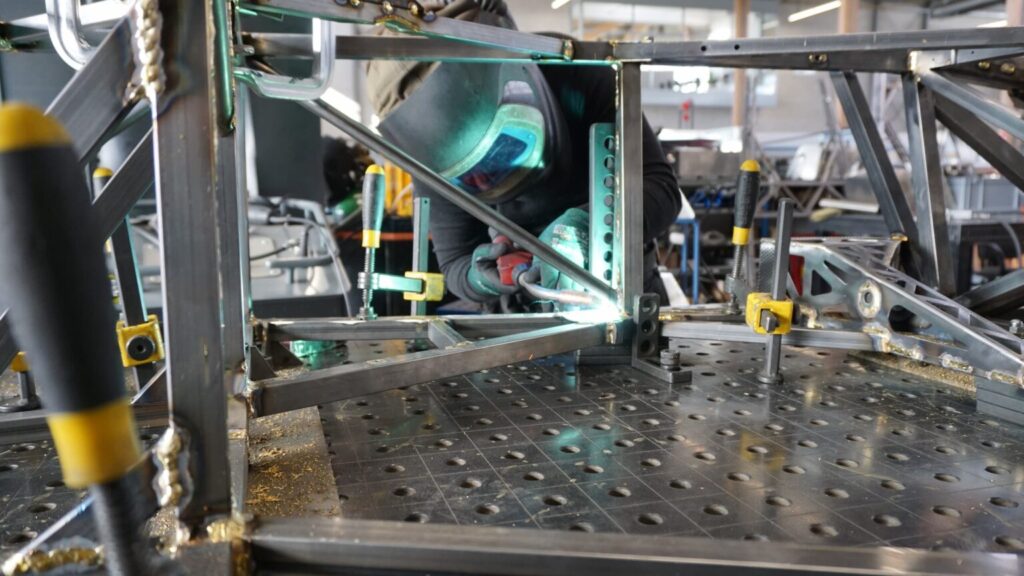
Het bouwen van een Donkervoort F22 is een zorgvuldig en gefaseerd proces dat zo’n twintig weken duurt. In kleine batches van drie auto’s doorlopen de voertuigen een reeks assemblagestappen. De ruggengraat van elke sportwagen is het chassis, samengesteld uit stalen buisframes en aluminium en carbon beplating. De stalen kokers en buizen die hiervoor nodig zijn, worden geleverd door Dumaco.
‘Ongeveer drie keer per jaar bestel ik alle onderdelen voor het chassis. Dat zijn ruim driehonderd onderdelen, die in series voor tien tot vijftien auto’s worden gesneden’, vertelt Leon Vergunst, verantwoordelijk voor het volledige operationele proces bij Donkervoort. De onderdelen komen als één snijpakket binnen en worden in de lasserij handmatig geassembleerd.
Ieder onderdeel op maat
Om foutloze assemblage te garanderen, zijn alle buis- en plaatdelen voorzien van unieke nokjes en gravures. ‘Hiermee zorgen we dat elk onderdeel precies op de juiste plek terechtkomt’, legt Vergunst uit. ‘Dat is noodzakelijk, want het chassis mag alleen in exact dezelfde vorm geproduceerd worden. Vanwege de typecertificering mogen we niets aanpassen zonder een volledige herkeuring.’
De assemblage gebeurt deels in mallen om de stijfheid en nauwkeurigheid te garanderen. Onder meer de voor- en achterkant, het bovendek en het motorframe worden in mallen gepositioneerd, waarna het geheel handmatig wordt koper- en soldeergelast. Daarna worden aluminium en carbon panelen aangebracht, inclusief een motorkruis in het motorruim voor extra stijfheid.
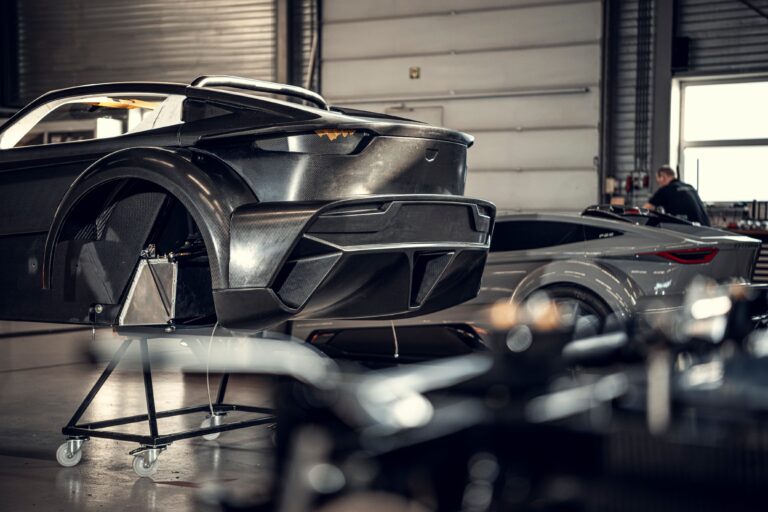
Maximale flexibiliteit, minimale marge
Hoewel de constructie van het chassis strak vastligt, is de rest van het voertuig grotendeels naar wens aanpasbaar. Klanten van Donkervoort kunnen hun auto tot in detail configureren. Van de demperinstellingen en het interieur tot het uitlaatsysteem en de kleur. ‘Elke klant koopt een productieslot en bepaalt pas vlak voor de bouw alle specificaties van de auto’, aldus Vergunst. ‘Dat vraagt om een flexibel productieproces, met een strakke aansturing via ons ERP-systeem.’
Die flexibiliteit vraagt ook veel van toeleveranciers. Dumaco levert geen standaarddelen, maar gesneden en gegraveerde componenten die volledig zijn afgestemd op het ontwerp van Donkervoort. ‘De marge om te corrigeren is klein. Alles moet in één keer passen.’
Slimme samenwerking
De samenwerking tussen Donkervoort en Dumaco is er een van wederzijdse afstemming en optimalisatie. Samen ontwikkelden ze gravures, nokjes en samenvoegmethoden die het assemblageproces versnellen en fouten voorkomen. Ook de materiaalkwaliteit en snijtechniek worden afgestemd op de vereiste sterkte en toleranties.
‘Voor ons is het essentieel dat een toeleverancier begrijpt wat er op het spel staat’, zegt Vergunst. ‘Een fout in het chassis is geen optie. Dankzij de samenwerking met Dumaco kunnen we die nauwkeurigheid waarborgen én tegelijkertijd efficiënt blijven produceren.’
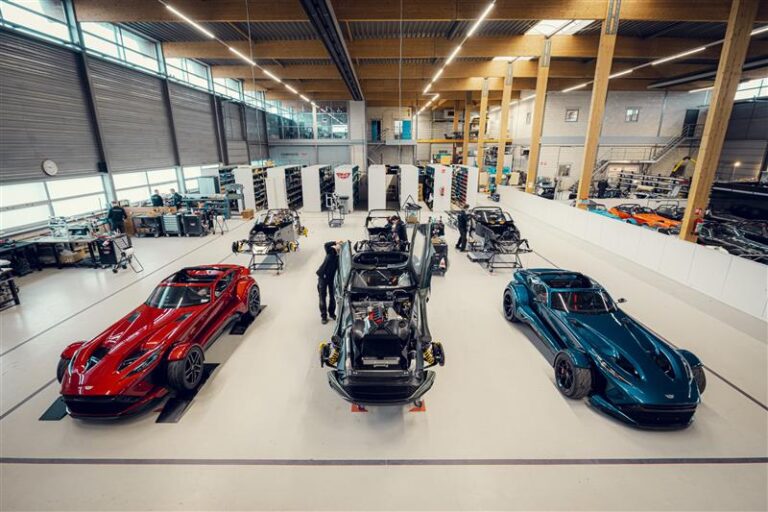