Toleranties: Iedereen met een technische opleiding kent ze. Hiermee wordt bedoeld dat maten in de praktijk altijd wat kunnen afwijken van wat de maat op tekening is. Dit komt niet alleen door de onvermijdelijke meetfout, maar ook door afwijkingen in de productie veroorzaakt door materiaaleigenschappen, instelling en afwijking van de machines en menselijke invloeden. Vaak geeft de tekenaar op een tekening aan hoeveel een maat in de praktijk mag afwijken van de maat op tekening. Dat noemen we toleranties.
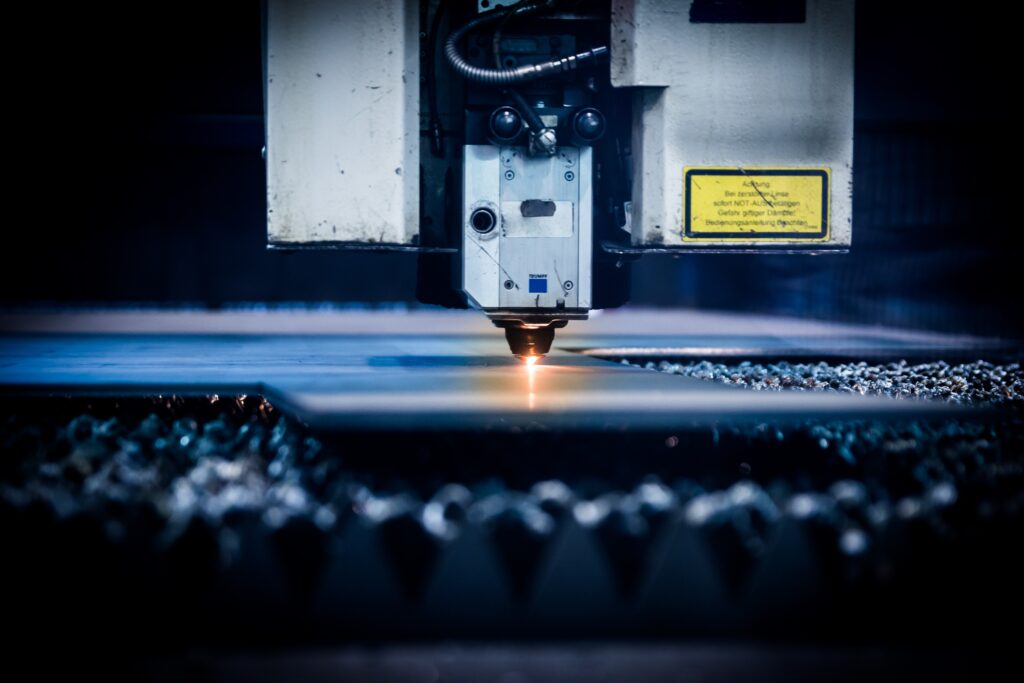
Maat- vorm- en plaatstoleranties
In de techniek dus geen probleem, zou je denken… Maattoleranties kent iedereen wel, maar er zijn ook vorm- en plaatstoleranties en dat is veel moeilijker. Vaak ontbreken deze op een tekening en als een product dan niet goed past, blijkt dat ze er hadden moeten zijn. Omdat alle producten uiteindelijk samengesteld worden uit meerdere delen, is het tijdens de productie (bij het lassen of assembleren) van belang dat de productdelen goed op elkaar passen. Maar omdat productonderdelen vaak in verschillende fabrieken worden gemaakt, moet de ontwerper van het eindproduct goed weten welke toleranties zijn toegestaan.
Maar het is nog lastiger. Tijdens productie kunnen maten gaan ‘verlopen’, ofwel verder gaan afwijken. Dat kan komen door slijtage van machines, gereedschappen of mallen. Degene die deze producten maakt, merkt het niet. Immers zijn proces is goed ingesteld en dus produceert men lekker door. Degene die het product moet samenstellen, merkt dat het steeds minder goed gaat passen. Wil je als bedrijf een goede kwaliteit (blijven) leveren, dan is het handig om niet het eindproduct te meten, maar tussen alle fabricagestappen. Toch? Maar alles meten is erg duur en vertraagt het productieproces.
Toleranties Vooraf meten
Maar hoe dan? Het uitgangspunt van alle kwaliteitssystemen is dat afwijkingen (dus maten die buiten de tolerantie vallen) zo snel mogelijk opgemerkt worden. Toch wil je niet alles hoeven meten. Meten kost geld en kan ook weer fouten opleveren.
De ISO-9001 geeft hiervoor een goed middel dat erg ondergewaardeerd wordt: de risicoanalyse per bepalende processen. De bedoeling van deze analyse is om tevoren te overdenken waar afwijkingen in een proces kunnen optreden en hoe deze herkent en/of vermeden kunnen worden.
Een simpel voorbeeld is de productie van een rechthoekig plaatje met een gat er in. Als dit geheel handmatig gemaakt wordt met een schaar en een boormachine, is de nauwkeurigheid van alle maten volledig afhankelijk van de ervaring en kunde van degene die de bewerking uitvoert, de nauwkeurigheid van de schaarbladen, de kwaliteit van boor en boormachine. Toleranties zullen in millimeters liggen, ook nog afhankelijk van het tijdstip van productie (maandagochtend etc). Wordt het plaatje daarentegen geheel door een lasersnijmachine gesneden uit volle plaat, zullen alle maatafwijkingen maximaal 0,01 mm zijn, de afwijking van de lasersnijmachine. Dus als de toleranties van alle maten door de ontwerper groter zijn dan 0,01 mm, hoeft de laseroperator niet te meten, immers het programma is goed en de afwijking is minder dan de toegestane tolerantie. En de laserstraal slijt niet, dus is er geen verloop van het proces. Wel kan de instelling van de bundel gaan afwijken en dan zal de snede slecht zijn. Dit kan eenvoudig visueel waargenomen worden. Dus als de laseroperator het juiste programma, materiaal en instelling heeft gecontroleerd (eerste productcontrole), hoeft de operator alleen nog de snede visueel te beoordelen of de instelling nog goed is.
Dit eenvoudige voorbeeld laat zien wat ik bedoel. Als je weet wat de mogelijke afwijkingen van een proces zijn, kan je een effectief meet- of controlesysteem opzetten voor dat proces. Wel zijn hiervoor twee zaken nodig: goede kennis van de eigen processen en kennis van alle toleranties bij de productontwerper of engineer. In de praktijk blijkt dit helaas zeer tegen te vallen.
Maar ook als je weinig kennis van de afwijkingen van processen hebt, kan je door middel van proeven, onderzoeken waar en hoe groot deze afwijkingen zijn. Hiervoor zijn een groot aantal statistische kentallen te gebruiken, maar met simpele beredenering kom je er in de praktijk ook wel. Voorbeelden zijn het Cpr kental of SPC (Statistical Proces Control). Met Cpr kan je de stabiliteit van het proces tevoren bepalen, met SPC kan je gedurende het proces afwijkingen monitoren om zo op tijd bij te kunnen sturen. Als dit goed toegepast wordt, zijn dit relatief simpele methoden met zeer positieve effecten.
Jammer is dat deze risicoanalyse in de praktijk eigenlijk niet goed gebruikt worden, terwijl deze moeite later veel geld kan besparen: meetkosten en foutkosten. Veel bedrijven zien de risicoanalyse van de ISO-9001 als een verplicht nummertje en proberen het zelfs van een ander bedrijf te kopiëren. Dit ontneemt hen een krachtige methode om meet- en foutkosten te besparen op de langere termijn.
Ook de kennis van toleranties bij ontwerper en engineers is vaak onvoldoende. Vooral maattoleranties bij onderling bewegende delen (wie kent nog het genormaliseerd passingstelsel of kan het toepassen?) leveren veel problemen op en sommige ontwerpers laten het dus maar gewoon weg op tekening. Bij vorm- en plaats toleranties is het nog erger, deze ontbreken vrijwel altijd.
Kortom er zijn veel methoden om meet- en foutkosten te minimaliseren, maar deze vereisen wel kennis van zaken. Veel problemen in de productiepraktijk zijn echter tot dit kennisgebrek te herleiden.
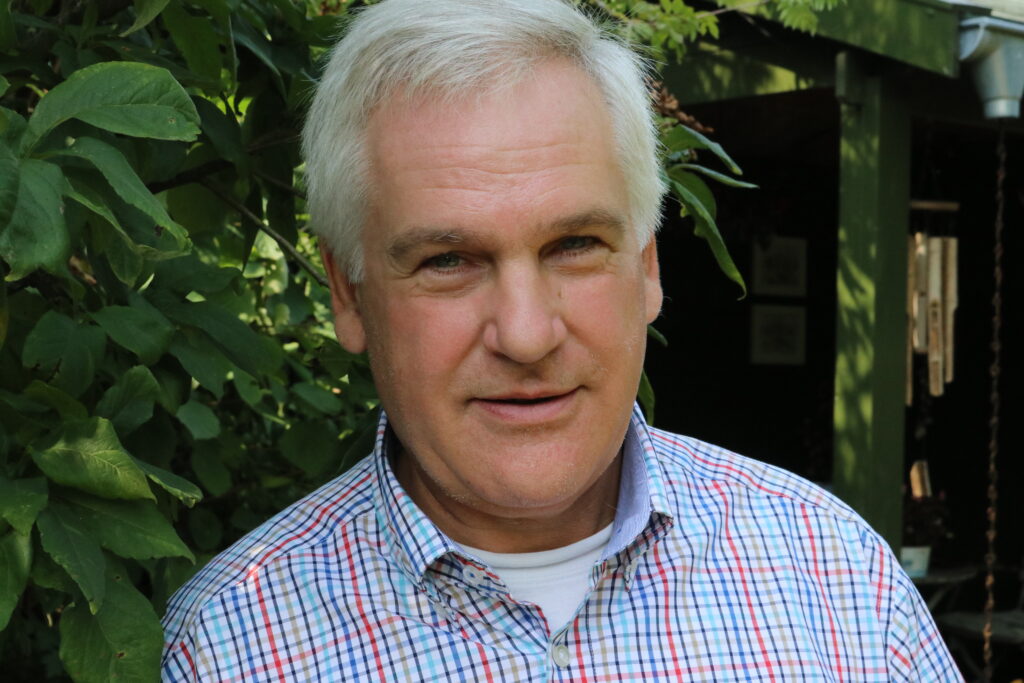