Bij gasfasedepositie wordt er een dunne laag gevormd op een substraat. Er zijn twee soorten gasfasedepositie: fysische gasfasedepositie (PVD, physical vapor deposition) en chemische gasfasedepositie (CVD, chemical vapor deposition). De deklagen die met gasfasedepositie worden gemaakt, zijn meestal dun, variërend van enkele nanometers tot maximaal een paar micrometers. Omdat de lagen laag voor laag worden opgebouwd, zijn dikke lagen kostbaar, is het moeilijk om de juiste groei en structuur te behouden, en hebben ze vaak geen praktisch nut.
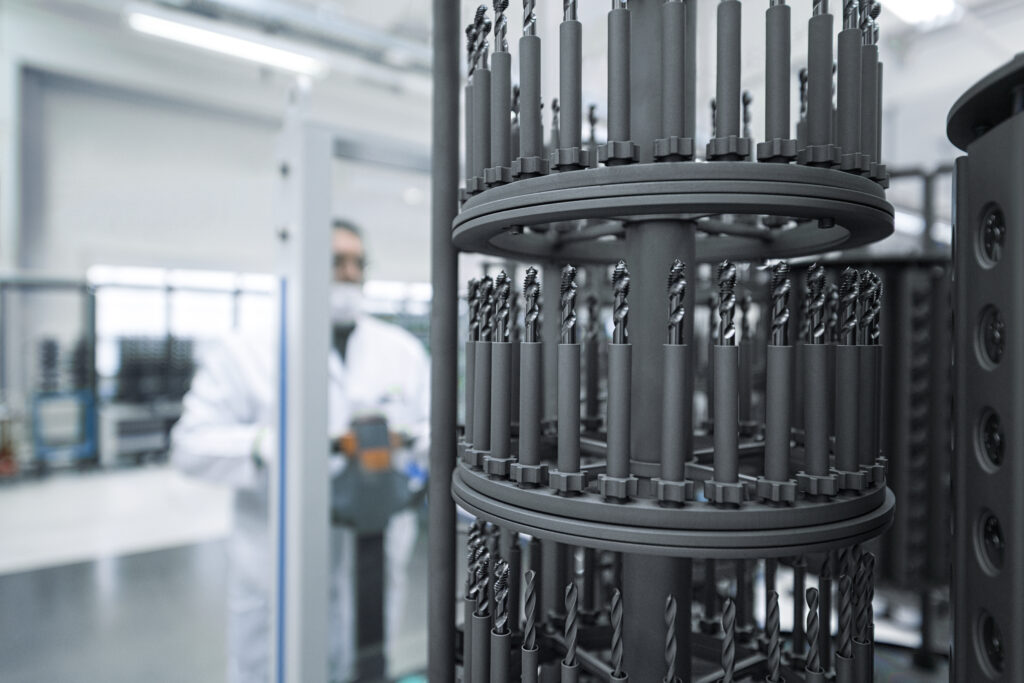
Verschil tussen PVD en CVD
PVD coating is een proces dat afhankelijk is van directe bestraling. De damp wordt alleen afgezet op plaatsen die direct zichtbaar zijn vanaf de bron. Dit kan gedeeltelijk worden gecompenseerd door driedimensionale objecten te laten bewegen ten opzichte van de bron. Een voordeel van CVD is dat de deklaag wordt afgezet op alle plaatsen waar de gassen kunnen komen. Bij het aanbrengen van een titaannitride-laag door thermische CVD met behulp van titaanchloride en stikstof zijn temperaturen van meer dan 1000 °C vereist. Er zijn echter ook precursorstoffen die bij kamertemperatuur al een aluminiumlaag kunnen afzetten. Bij grootschalige industriële toepassingen van het coaten van vensterglas, zowel op grote formaten als op grote schaal, worden zowel PVD als CVD gebruikt. CVD heeft een kostenvoordeel wanneer het direct in de glasoven wordt uitgevoerd. Offline zijn de kosten ongeveer gelijk, maar vaak wordt de voorkeur gegeven aan PVD omdat het als flexibeler wordt beschouwd in termen van verwerking.
Toepassingen van PVD & CVD
Oppervlaktetechnieken spelen een grote rol in ons dagelijks leven. Dit geldt ook voor coatings die gebaseerd zijn op PVD en CVD. Echter, meestal worden ze over het hoofd gezien of kijkt men er doorheen:
Bijna alle vensterglas wordt gecoat met PVD of CVD om de lichtdoorlaat en warmte-isolerende werking te vergroten.
Onderdelen van (diesel)motoren worden gecoat met een slijtvaste keramische laag; zonder deze coatings zou de zuinige dieselmotor niet kunnen functioneren. Een goed voorbeeld van deze zwaar belaste onderdelen zijn tandwielen, kleppen, lagers en assen in zware voertuigen.
Oppervlakken van kunststof worden met metaal gecoat om reflectie, geleiding of een fraai uiterlijk te krijgen. Onderdelen voor optische systemen worden gecoat om juist geen reflectie te hebben.
Onderdelen van cosmeticaverpakking krijgen met een dunne metaallaag een dure uitstraling. Ook folie en papier worden met PVD gecoat, als fraai verpakkingsmateriaal, maar ook voor de conserverende barrière-eigenschappen van de coating in bijvoorbeeld zakken voor levensmiddelen.
In de duurzame energiesector, bijvoorbeeld bij zonnepanelen, wordt een aantal processtappen met behulp van PVD en CVD uitgevoerd. Ook voor toepassingen in de zorg of de medische wereld, worden steeds meer PVD en CVD coatings gebruikt. Scherpe snijvlakken van medische instrumenten zorgen er voor dat wonden sneller helen terwijl de antibacteriële eigenschappen de kans op infecties verkleinen en hersteloperaties voorkomen.