De productie van composieten elementen vereist specialistische kennis van vezels en mallen, en van harsen, lamineren en uitharden. Maar ook tijdens het nabewerken is veel kennis nodig. Het frezen van composieten bijvoorbeeld, kun je niet hetzelfde benaderen als het frezen van staal, of van kunststof, zoals soms wordt gedacht. Joop Lahm adviseert composietverwerkers in Nederland en kent ondertussen het klappen van de zweep.
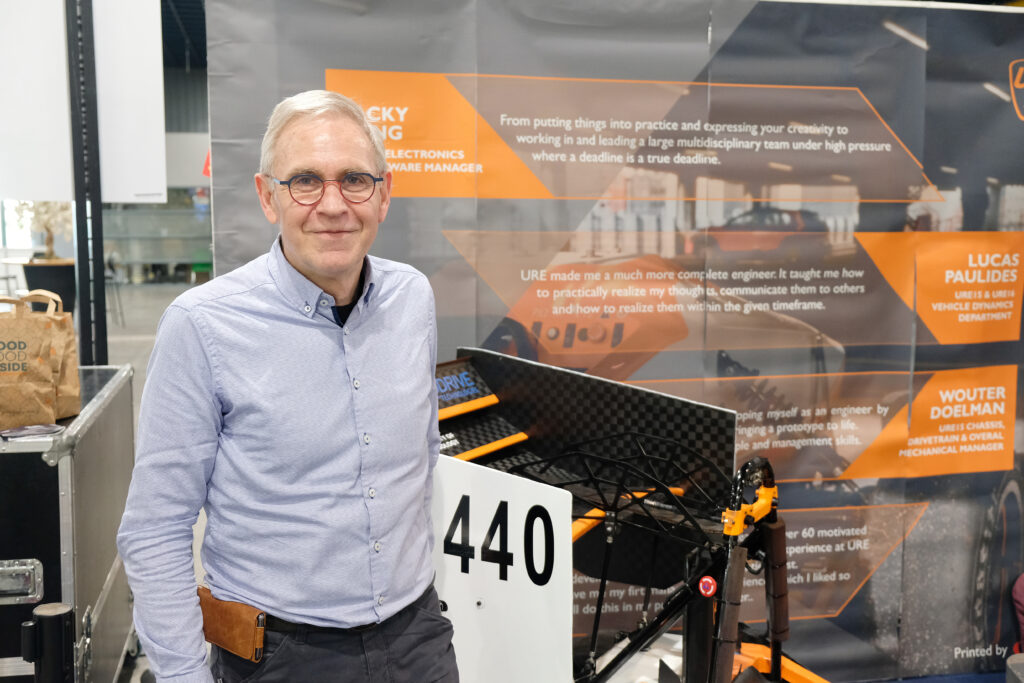
Als een composieten element is uitgehard, is het materiaal op de meeste plekken even dik. Maar aan de randen van de mal lopen de vezels wat af. Omdat je overal je kwaliteit wilt behouden, moet je die buitenste rand eraf halen. Frezen. Daar houd je al rekening mee bij je ontwerp. Het product wordt iets groter dan nodig, zodat je genoeg overhoudt na het frezen. “We proberen natuurlijk zo min mogelijk verlies te hebben. Want je moet het materiaal er eerst instoppen en later weer vanaf halen. Maar je moet toch wel rekening houden met een verlies van 5 tot 10%”, vertelt Lahm, die met zijn bedrijf CNC Freestechniek andere bedrijven adviseert op het gebied van gereedschappen en freesstrategieën.
Niet te voorspellen
Eén van Lahm’s klanten maakt grote onderdelen. “Segmenten van een meter of 2. En acht van deze segmenten vormen samen een bol. Er zit een overmaat op van 30 millimeter aan iedere kant en dat willen ze terugbrengen naar 25 mm. Maar je moet wel zeker weten dat er aan het eind van het proces genoeg materiaal overblijft”, illustreert hij. Want het is nooit helemaal te voorspellen hoeveel materiaal je er precies weer af moet halen. Als het lukt de overmaat te verkleinen, is er minder composiet nodig voor de onderdelen. Allemaal kostenbesparing.
In kaart brengen
Welke vraagstukken kom je tegen als je composieten gaat verspanen? Je moet eerst in kaart brengen waar je mee te maken hebt, vertelt Lahm. “Wat voor vezels zijn er gebruikt? Wat is de dichtheid van de vezels en de richting van de vezels? Qua verspaning komt dat allemaal net anders uit. Als je parallel aan de vezel of er recht op gaat snijden, of zelfs in een hoek van 45 graden, het vergt allemaal een andere aanpak.” Een gewone frees heeft een spiraal met een snijkant. Recht toe, recht aan. Maar voor composieten ziet dat er anders uit, ingewikkelder. “We hebben hier roughers en een soort vertanding die de vezel omhoog drukt maar langer vasthoudt”, zegt hij, wijzend op een speciale frees voor composieten. “Het moet een neutrale snede zijn, er wordt niet aan getrokken. Want anders krijg je last van delaminatie. De composiet bestaat uit laagjes, vezels en een matrix. De matrix kan een hars zijn of een thermoplastische kunststof. Het heeft de neiging los te gaan. Dat moet je zien te voorkomen, want dan raak je sterkte kwijt. Met deze speciale frezen garandeer je dat de vezel wordt afgesneden. Maar glas/epoxy gedraagt zich anders dan een PEEK met koolstof. En ook weer anders dan een PP met glas, wat je in de automobielindustrie steeds meer ziet.” Elke combinatie van vezels en kunststof vereist weer een andere freesstrategie.
Thermoplasten
Omdat composiet zo’n algemene term is en er zoveel variaties mogelijk zijn, is het ook niet altijd gelijk duidelijk welke tactiek je het beste kunt toepassen. “Iemand kan besluiten koper toe te voegen, of een deel Kevlar, een deel glas en een laag koolstofvezel erbovenop. Dan wordt het een hele ingewikkelde constructie”, weet Lahm. In Nederland ziet hij trouwens steeds vaker dat er met thermoplasten wordt gewerkt. Veel meer dan in Duitsland. “Samen met een Nederlandse klant hebben we frezen ontwikkeld speciaal voor thermoplasten.” CNC Freestechniek is vertegenwoordiger van het Duitse Hufschmied, dat gereedschappen voor composieten ontwikkeld. Die hebben nu ook de frezen voor thermoplasten in hun assortiment opgenomen.
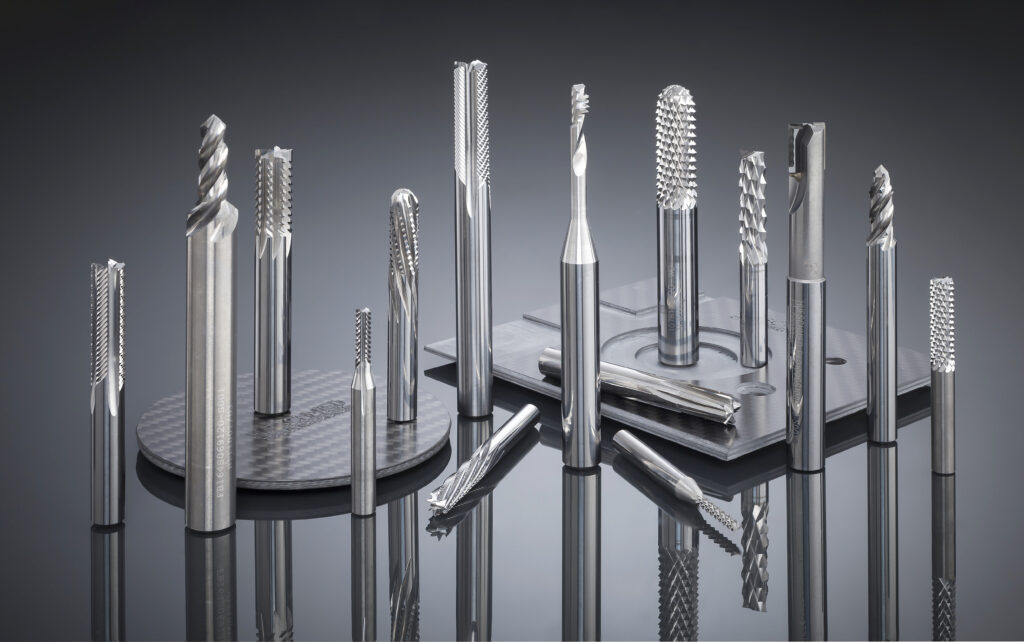
Andere methode
Ziet Lahm het nog vaak misgaan? “Ja, heel vaak. Dat komt ook omdat mensen bijvoorbeeld uit de metaal ineens composiet gaan frezen, en dat vergt een hele andere aanpak. De snelheden zijn anders, de voedingen zijn anders. En de strategie is anders. Het frezen van composieten doen we het liefst op een vijf-asser. Want je wilt haaks op de vezelrichting staan. En als het product een ronding heeft, wil je met je frees met die ronding meegaan. Als je niet via de juiste kant het materiaal benaderd, is dat zwaar voor de frees. Je hebt een hele lange snijkant nodig, met instabiliteit als gevolg. Want het materiaal is erg sterk. Dat vergeet je snel, maar 4 mm composiet komt soms overeen met 12 mm staal. Dat is verraderlijk.” Bij thermoplasten moet je goed opletten dat je materiaal niet te heet wordt. Daar heb je bij thermoharders minder last van, hoewel dat wel kan branden. “Bij thermoplastisch composiet is de matrix echt de leidende factor”, legt Lahm uit. “Het is niet de wrijving die zorgt voor de opwarming van het materiaal, het is de spaanvorming, het afsnijden van het materiaal. Daar zit de energie in en die wil je met de spaan mee weg hebben. Ga je te langzaam, dan stop je er sowieso te veel warmte in.”
Sandwichmaterialen
Naast matrix en vezels heb je ook nog eens te maken met de opbouw van de composiet. “We komen vaak sandwichmaterialen tegen. Bijvoorbeeld in de automobielindustrie, de zijwanden van vrachtwagens, is een combinatie van glasvezelversterkt epoxy aan de buitenkant, met een gelcoat eroverheen, voor glans. Dan een laag schuim en dan weer diezelfde glasvezelepoxy met een gelcoat. Dat moet in één keer verspaand worden en dat is een uitdaging. Want het zijn compleet verschillende materialen die ook compleet anders verspaand willen worden. We komen ook materialen tegen met koolstofcomposiet aan de bovenkant, aluminium honingraat binnenin en dan weer koolstofcomposiet, voor militaire toepassingen. Of honingraat dat is opgebouwd uit een PP-deklaag met glasvezel erin. Dan een PP-honingraat en dan weer een PP-deklaag. Wéér een andere technologie.”
Probleem
Het tegelijkertijd frezen van hardere en zachtere materialen kan voor problemen zorgen. Soms moet je besluiten de glascomposiet eerst weg te halen, om het schuim binnenin apart te frezen. Schuim is bij voorkeur recyclebaar, een PET-foam is dan geschikt. “Maar die smelt bij 60 graden. Dat kan ik niet realiseren in mijn glasvezelgedeelte. Het is steeds weer een uitdaging om iets te vinden wat lukt.” Lahm besluit: “En soms lukt het ook niet. Dan moet je meerdere stappen zetten.”