Bij het binnenstappen van de ontvangsthal van GOMA in Hengelo (Gelderland) ademt alles nog historie. Maar schijn bedriegt. Achter die eerste indruk schuilt een moderne, sterk geautomatiseerde fabriek die de afgelopen jaren ingrijpend vernieuwde.
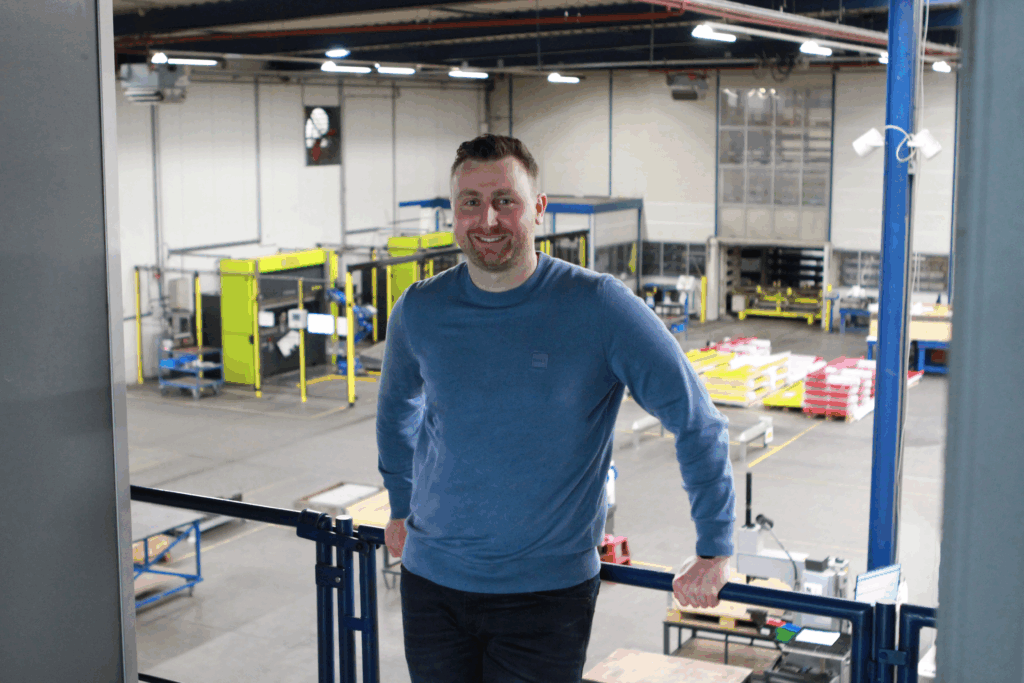
Directeur Tom Kreunen (36) zag GOMA in de elf jaar dat hij er werkt veranderen van een traditionele toeleverancier in een gestroomlijnde moderne fabriek. ‘Zo’n zeven jaar geleden zijn we vrij voortvarend aan de slag gegaan om dat traditionele er maar eens uit te halen. Door eigenlijk op een heel andere manier te gaan produceren’, vertelt hij.
Kreunen schetst hoe GOMA eerder kampte met veel onderhanden werk en een lage doorstroom. ‘De voorraden stonden tot aan het dak.’ Ook de routing door de fabriek liet te wensen over. Allemaal zaken die de afgelopen jaren zijn aangepakt.
Logische routing
Op een ingelijste luchtfoto toont Kreunen hoe het bedrijf sinds de oprichting in fases steeds verder werd uitgebreid. Vanwege de landelijke omgeving moest het pand er in eerste instantie uit zien als een boerenbedrijf. Later werd dit losgelaten en kwam er zo’n 14.000m2 aan ruimte bij. ‘Het nadeel van stapsgewijze uitbreiding is dat je vanzelf structuur kwijtraakt’, zegt Kreunen. ‘Daarom zijn we de afgelopen jaren opnieuw gaan kijken naar hoe het werk zich door de fabriek beweegt.’
Een van de grootste veranderingen was het aanbrengen van een logische productieroute. ‘We hebben heel veel machines verplaatst om het proces zo in te richten dat het materiaal in één richting door de fabriek gaat. Het maakt als het ware een U-beweging door het gebouw: de plaat komt binnen, wordt stap voor stap bewerkt, en verlaat het pand vrijwel op dezelfde plek als eindproduct.’
Minder zoeken
Maar machines verplaatsen alleen was niet voldoende. Ook in de logistiek viel winst te behalen. ‘Je ziet dat er gewoon heel veel tijd en energie verloren ging aan de logistieke handelingen, dus dat wilden we zeker niet vergeten in het stukje robotisering en automatisering. Dankzij de opeenvolgende bewerkingen konden we overal stations creëren waar de AGV langs kan rijden. Daar staat het werkstuk dan naast het pad, zodat de operators het er zo vanaf kunnen pakken en weer verder kunnen op hun plek’, wijst Kreunen op een foto van een Kumatech AGV aan de muur.
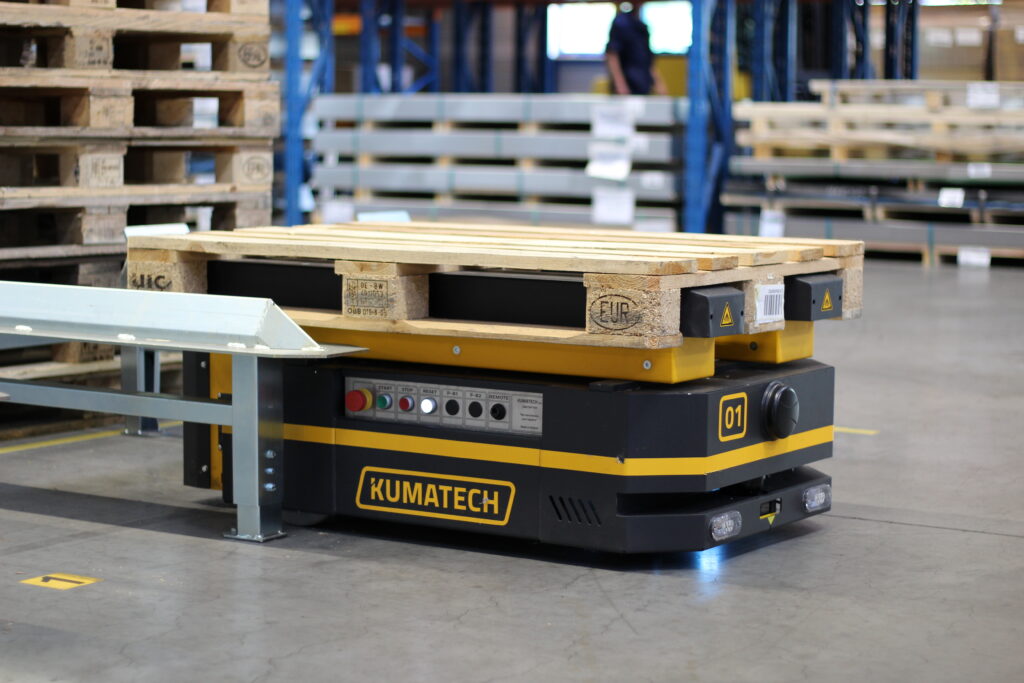
Juiste keuzes
Ook de planning is aangepast aan de nieuwe structuur. ‘Een jobshop omgeving zoals wij hebben is best moeilijk te plannen. Het gaat om honderden orders tegelijkertijd, die allemaal verschillende routes afleggen. Dat is voor een mens moeilijk om te overzien en om op de juiste manier te handelen.’ De oplossing kwam zo’n twee jaar geleden met de overstap op nieuwe planningssoftware. ‘Die helpt ons de juiste keuzes te maken zodat de doorstroom behouden blijft. De juiste orders op het juiste moment op dezelfde plek zeg maar’, vertelt Kreunen, die aangeeft dat er vooral in leverbetrouwbaarheid hierdoor grote stappen vooruit gezet zijn.
Daarmee ging ook de productiviteit van de medewerkers omhoog. ‘Voorheen waren operators veel tijd kwijt aan zoeken: een kanter reed met de heftruck door het bedrijf op zoek naar zijn werkstuk. Nu hebben we één logistieke medewerker die dat verzorgt. Als de kanter zich omdraait, ligt zijn volgende order al klaar. De kanter is weer aan het kanten, de lasser aan het lassen.’
Toegevoegde waarde
De veranderingen op de werkvloer vloeiden voort uit een bredere koerswijziging die GOMA enkele jaren geleden inzette. In de nasleep van corona beleefde het bedrijf in 2021 en 2022 de drukste jaren ooit. ‘Een klant van ons maakt bijvoorbeeld koelkasten voor campers en caravans. Dat was toen booming, daardoor ging het echt heel hard’, vertelt Kreunen. De vraag was zo groot dat er geen ruimte meer was om al het werk uit te voeren. ‘Toen zijn we heel kritisch naar onze klanten gaan kijken. Wat past nou eigenlijk wel bij ons en wat niet?’
De focus kwam te liggen op werk met toegevoegde waarde. ‘We hebben een poedercoatlijn en doen assemblagewerk – juist dat type werk past bij ons. Maar we hadden ook veel klanten die alleen snij- of kantwerk bij ons onderbrachten,’ zegt Kreunen. GOMA ging in gesprek met deze klanten om aan te geven dat hun werkzaamheden niet meer aansloten bij de richting die het bedrijf op wilde. ‘Die gesprekken waren niet makkelijk, maar wel nodig’, zegt Kreunen. ‘We wilden minder bulk, en meer projecten waarin we echt iets kunnen bijdragen.’

Mindere tijden
In overleg met klanten werd het werk geleidelijk afgebouwd en overgedragen aan andere plaatbewerkers, waar al met al bijna anderhalf jaar overheen ging. Toen ontstond er eindelijk ruimte voor het soort werk dat GOMA juist wél wilde doen – ware het niet dat op dat moment de markt begon af te koelen. Precies in die periode, zomer 2023, nam Tom Kreunen het stokje over als directeur. In eerste instantie nog samen met Adelin Lankveld, sinds begin dit jaar staat hij alleen aan het roer.
Hoewel de omzet destijds met maar liefst acht miljoen euro terugliep, kwamen er geen gedwongen ontslagen of reorganisatie. ‘Dat past ook niet echt bij de filosofie van de stichting, zegt Kreunen, die toelicht hoe het familiebedrijf in 2012 – bij gebrek aan opvolging – werd overgenomen door de speciaal daarvoor opgerichte stichting Stimeta (Stichting Metaal Achterhoek). Die stichting richt zich op continuïteit en behoud van werkgelegenheid voor de regio. Dat is dus gelukt.
Personeel denkt mee
‘Er gingen in die periode best wat mensen met pensioen. Die zouden we normaal gesproken vervangen, maar dat hebben we nu bewust niet gedaan’, legt Kreunen uit. Zo kromp het personeelsbestand zonder gedwongen ontslagen. Tegelijkertijd werd er gekeken naar het omlaag brengen van kosten. ‘We hebben medewerkers bewuster gemaakt van hun energieverbruik – zoals het uitschakelen van machines tijdens pauzes. Maar we hebben hen ook actief om ideeën gevraagd.’
Dat leverde praktische besparingen op. Ritten die eerder werden uitbesteed, doet GOMA nu weer zelf. Onderhoudsbeurten aan machines zijn – in overleg met leveranciers – uitgesteld, omdat de gebruiksduur tijdelijk lager lag. ‘Alles bij elkaar levert dat best wat op,’ aldus Kreunen.
Blijven investeren
Toch werd er niet enkel bezuinigd, er werd ook nog gewoon geïnvesteerd in automatisering en robotisering. Dit maakte het mogelijk om hetzelfde werk te doen met minder mensen. Zo schafte GOMA bijvoorbeeld een laserlascel met cobot aan.
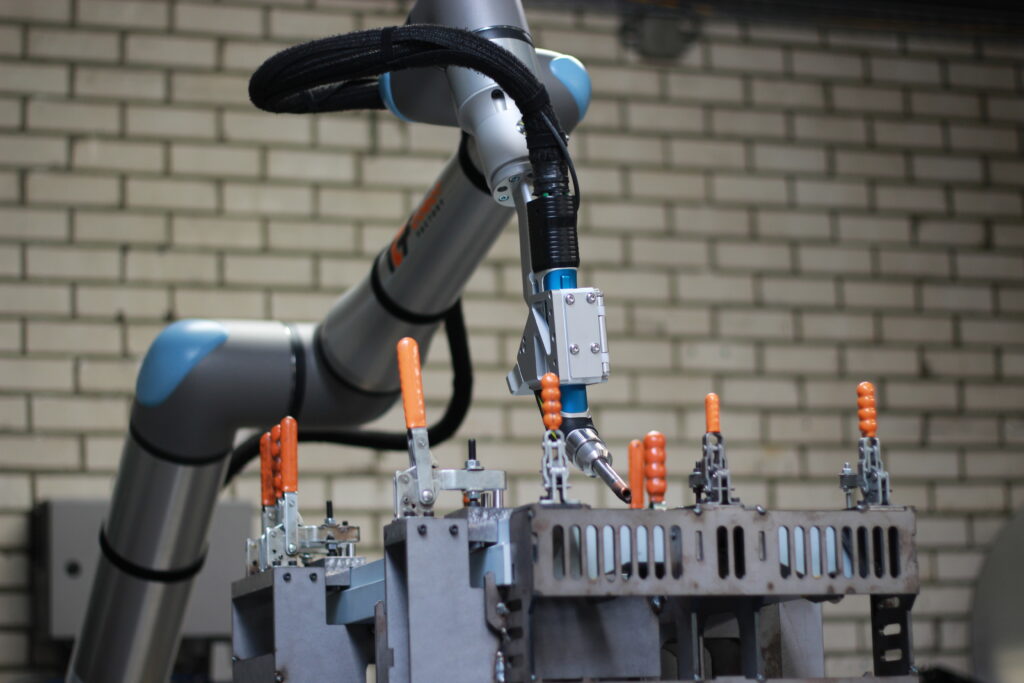
‘We hebben eigenlijk altijd met robots gewerkt en vaak kwam wel de vraag, moeten we niet iets met een cobot doen? Voor het laserlassen leek een cobot een mooie oplossing, omdat de drempel om hem te programmeren laag is’, vertelt Kreunen, die aangeeft dat GOMA veel dun aluminium last, wat niet zozeer constructief is. ‘Het gaat bij ons vaak om cosmetische lassen,’ legt Kreunen uit. ‘Hoeken moeten mooi gesloten zijn, niet per se supersterk. We bouwen geen bruggen of schepen.’
Bij MIG- of TIG-lassen leidde dat vaak tot vervorming, met als gevolg extra slijp- of afrondwerk. De overstap naar laserlassen bracht daarin verandering. ‘Met laserlassen blijven de naden veel strakker, en in veel gevallen is nabewerken niet meer nodig,’ zegt hij. ‘Het scheelt tijd, en het eindresultaat is gewoon mooier.’
Voorbereid op de toekomst
Een andere recente investering is de nieuwe poedercoatcabine. Met deze installatie kunnen kleuren sneller worden gewisseld, wat de omsteltijden verkort en de capaciteit verhoogt. De cabine is al voorbereid op de komst van een spuitrobot, die in de toekomst het handmatige bijspuiten overneemt.
De robot wordt straks aangestuurd via een scanner die herkent welk product eraan komt en in welke positie het hangt. Omdat veel producten repeterend zijn, is één keer programmeren meestal voldoende. Daarna past het programma zich automatisch aan op de manier waarop het product is opgehangen.
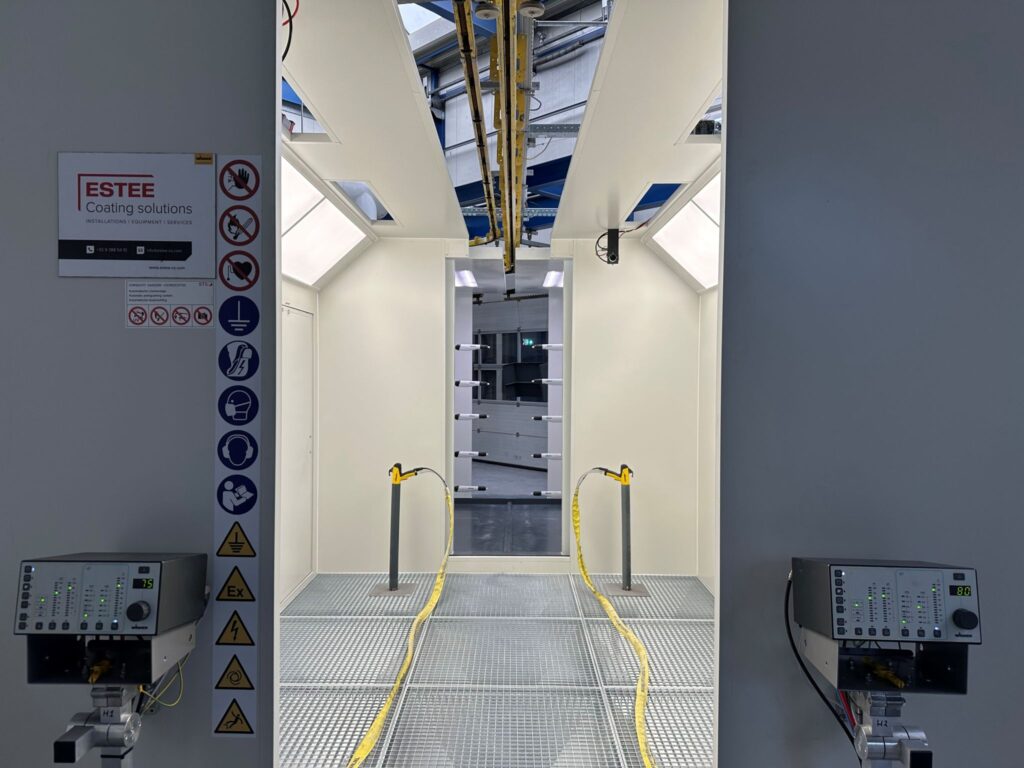
Ophangen zonder stress
Een van Kreunens toekomstplannen is het automatiseren van het ophangen aan de lakbaan. Nu gebeurt dat nog handmatig, wat zowel fysiek als mentaal (door de tijdsdruk) belastend is. ‘Het is zwaar werk dat vaak door jonge mensen gedaan wordt. Maar dat zijn tijdelijke krachten, en die moet je telkens opnieuw inwerken,’ zegt Kreunen.
Het idee is dat producten straks direct na het kanten of lassen aan een drie meter lange traverse gehangen worden, die via een AGV naar een automatisch buffermagazijn gaat. Daar blijven ze tijdelijk opgeslagen tot ze op het juiste moment automatisch aan de lakbaan worden gekoppeld. ‘Dat belast de medewerkers minder.’
Saamhorigheid
Want daar draait het uiteindelijk om: automatisering en robotisering moeten het werk lichter maken, zodat er ruimte ontstaat voor werk waar de medewerkers energie van krijgen. Een belangrijk doel voor de komende jaren is dan ook om het werkgeluk te vergroten en de saamhorigheid te versterken. ‘Vorige week hielden we een klusmiddag. De productie lag even stil, iedereen ging aan de slag: schilderen, schoonmaken, verlichting vervangen. Geen groot project, maar het gaf meteen dat oude gevoel van samen iets doen. Dat het ook gewoon leuk is om hier te zijn.’ Met een nieuwe lik verf, een gestroomlijnde fabriek en een duidelijke koers ligt de basis voor een mooie toekomst voor GOMA.