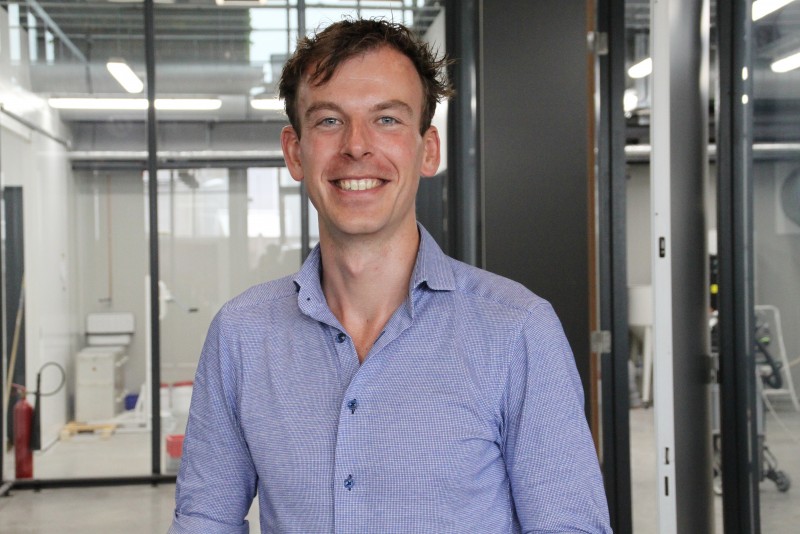
Parts on Demand is in februari 2019 verhuisd van Tiel naar de Oude Werkspoor fabriek in het Werkspoor Kwartier in Utrecht. ‘Honderd jaar geleden begon daar de tweede industriële revolutie en wij hopen met 3D-print mee te werken aan de vierde industriële revolutie’, aldus Neil van Es van Parts on Demand. De ondernemer vertelt over zijn ambitie te groeien van zo’n 15.000 3D-geprinte producten per week naar 2,5 miljoen onderdelen per jaar.
Van Es kwam tijdens zijn studie Werktuigbouw en Industrieel ontwerp in Eindhoven met zijn bedrijf Vesco (van Van Es en Co) voor het eerst in aanraking met 3D-print. Eerst nog een eenvoudige 3D-FDM-printer, waarmee Vesco prototypes maakte voor zijn klanten. Van Es: ‘Op een zeker moment kregen we opdracht onderdelen te 3D-printen voor in een serie airco’s. Dat ging best goed, de onderdelen hielden zich prima. Dat leverde steeds meer werk op, maar met de FDM-printer liepen we tegen grenzen aan qua sterkte en productievolume. Daarom besloten we het 3D-printwerk uit te besteden. Na een tijdje liepen we tegen de lange levertijden aan en hebben we de stap gemaakt zelf een professionele SLS 3D-kunststofprinter aan te schaffen. Dat was een tweedehands instapmodel van het Duitse EOS. Dat was een goede beslissing want al na een half jaar was deze machine voor de rest van het jaar vol gepland’, zegt Van Es.
Verhuizing
‘Toen hadden we de keus, of terug naar de toeleverancier of een extra 3D-printer te kopen. Dat was een paar maand voor FormNext 2017, de vakbeurs voor additieve productie in Frankfurt (red.: de eerstvolgende FormNext is van 18-22 november 2019). Op die beurs hebben we een grotere versie – de EOS P396 – besteld waarmee we met kunststof poeders producten konden 3D-printen tot een formaat van 320 bij 320 bij 600 mm.’
Omdat het 3D-printen een steeds grotere plek begon in te nemen besloot Van Es in 2018 de bedrijfsnaam te veranderen in Parts on Demand. Zo groeide het bedrijfje binnen vier jaar van op een studentenkamer producten ontwikkelen, prototypes bouwen naar de serieuze productie met 3D-kunststofprinters. Februari dit jaar verhuisde het bedrijf van Tiel naar Utrecht. ‘Met deze verhuizing hebben we gigantisch veel gewonnen qua efficiency. De hele productierouting is logischer ingedeeld waardoor we meer halen uit onze machines dan een jaar geleden. Zo is de uitval van onze machines fors verlaagd. Dit was voorheen zo’n tien procent, nu is dat minder dan één procent. Sinds maart van dit jaar tot nu (eind juli) hebben we geen uitval gehad.
Een medewerker van Parts on Demand bekijkt een van de EOS 3D-printers.
De 3D-printers
Met de verhuizing heeft Parts on Demand de ruimte en de ambitie te groeien naar acht printers en daarmee de productiviteit op te voeren naar 2 tot 2,5 miljoen producten per jaar. Dat zullen ook weer EOS-machines worden. Van Es: ‘Sterker, dat zullen precies dezelfde machines worden. Een ander merk of type betekent extra werk en tijd om die machine eigen te maken.’ Een groter formaat wil de ondernemer ook niet. Hij vindt dat de huidige afmetingen een mooie balans vormt tussen flexibiliteit en productievolume. ‘Dat betekent snelle opstart van de 3D-printers en een relatief snel printproces met een hoge productiviteit. Bij een groter formaat machine krijg je te maken met batches die veel langer duren en heb je veel meer materiaal nodig. Het enige voordeel is dat we grotere producten kunnen maken. Maar we willen geen grotere producten maken. Grotere kunststof producten zijn namelijk gevoeliger voor krimp, krom trekken en torderen. Het grootste deel van onze markt zijn onderdelen binnen de 15 cm in het vierkant. Dat is qua kosten ook het meest economisch’, beargumenteert Van Es deze keuze.
Parts on Demand
Aantal medewerkers: 8 waarvan 1,5 fte productie en 6,5 in de engineering en verkoop.
Productie: Nu 10.000 – 15.000 producten per week in series van 1 tot 100.000 stuks. Een serie van 100.000 zal meer dan een week kosten om die uit te leveren.
3D-printers: 3 EOS 3D-SLS poederprinters
Nabewerkingen: stralen, kleuren (alle producten worden in wit 3D-geprint), veredelen en assemblage.
Groeiambitie: 2,5 miljoen onderdelen per jaar met 8 EOS-machines. Uitgaande van elke 9 maand een nieuwe machine, zou deze ambitie in 2022 kunnen worden bereikt. Van Es verwacht deze groei aan te kunnen met maximaal 12 tot 15 fte’s.
Klanten: Elke week een 40-tal orders van zo’n 30 klanten. Totale portfolio is 500 klanten.
Productieoppervlak: 400 m2
Printpoeders
‘We 3D-printen voornamelijk met de kunststof polyamide-poeders PA 11 en PA 12 (nylon). Dat is een hoogwaardige kunststof, die in steeds meer gevallen aluminium zou kunnen vervangen. Dat geldt zeker als je bij het verspanen het aluminium product één of meerdere keren moet omspannen. Dan zit er een mate van complexiteit in het product die je met een 3D-printer bij wijze van spreken gratis krijgt’, weet Van Es.
‘De polyamide (nylon) poeders die wij gebruiken zijn in 80 procent van de gevallen kwalitatief beter dan wordt gevraagd door de klant, maar toch doen we het dan in nylon. Dat is omdat al onze processen op dat materiaal zijn afgestemd. Omdat dit materiaal al heel lang wordt gebruikt in de 3D-printwereld heeft het vele certificaten, zoals voedselveiligheid, medisch en vlamvertragend. Doordat het veel gebruikt wordt, zijn PA-poeders qua prijs voordeliger dan een commoditykunststof als PP of ABS. Kijk die 3D-printpoeders zijn een stuk duurder dan granulaat. Vanwege de nauwe specificaties gaan die een paar keer over de kop. Ik denk dat PA 12 granulaat zo’n 5 tot 6 euro per kg doet, terwijl PA-poeders een veelvoud daarvan kosten, tot wel 63 euro per kg.’
Behind the Scenes
Om in contact te komen met de klanten en potentiële klanten organiseert Parts on Demand iedere twee maand een ‘Behind de Scenes’-middag waar klanten, leads en andere geïnteresseerden worden uitgenodigd om kennis te maken. En dat onder het genot van een biertje van onze buurbrouwer De Leckere’ en bitterballen. Dan laten we ze het hele proces zien en vertellen we over ontwikkelingen van materialen, nabewerking etc. De laatste was op 13 september. Dit was al weer de derde. De eerste was tijdens de opening in april en de tweede was in juni. Daar hadden we toch een opkomst van 40 belangstellenden. Daar hebben we zelfs een opdracht aan overgehouden van een meubelmaker annex sanitairbedrijf. Kijk voor die sector is 3D-print een oplossing om een product op de markt te brengen. Normaal gesproken als je een kunststof product op de markt wil brengen, moet je investeren in tooling en matrijzen. Dat is een lang traject met een hoog afbreukrisico. Met 3D-print kun je zo’n nieuw product in een kleine serie van 100 tot 400 stuks op de markt introduceren en kijken of het aanslaat, tegen beduidend lagere kosten.
PA mengen met carbonvezels
De kunststof poeders worden steeds hoogwaardiger, waardoor steeds vaker wordt gekozen voor het 3D-printen met PA-poeders. Aluminium wordt vaak gebruikt omdat het goed te verspanen is en lekker licht is, niet omdat je nu alle eigenschappen nodig hebt van aluminium. Aan de andere kant gaan de materiaalontwikkelingen in kunststof steeds verder. Zo is Parts on Demand bezig met proeven om carbonvezeltjes bij te mengen in de polyamide poeders en dit te 3D-printen. Hierdoor krijg je stijvere producten die thermisch beter belastbaar zijn en zelfs elektrisch geleidend zijn. De carbonvezels zijn net zo fijn als het poeder zodat bij het 3D-printproces het poeder om de carbonvezels heen smelt. Ook mag het poeder niet te glad zijn want dan hecht het poeder niet aan het carbon. ‘De kunst is om de carbon vezels homogeen door het poeder te krijgen en te houden. Dit is nog in ontwikkeling en we hopen daar over een paar maand meer duidelijkheid over te hebben’, denkt Van Es.
Poedergebruik
Parts on Demand verbruikt op jaarbasis ongeveer 18 ton PA-poeders. De restpoeders uit een eerder 3D-printproces worden gemengd met nieuwe poeders en gebruikt voor een volgende batch. Het is daarom ook een relatief duurzaam proces. ‘Van de 18 ton materiaal die we per jaar gebruiken, is 150 kg afval. Dat is best wel weinig’, vindt Van Es. ‘De poeders worden geleverd door de producenten van 3D-printers, in ons geval dus door EOS. Dat heeft ook weer met volume te maken.’
Neil van es (derde van links) met zijn medewerkers van Parts on Demand.
Engineeren en 3D-printen
‘Onze engineers betrekken de klant zoveel mogelijk in het proces zodat er een zo optimaal mogelijk product ontstaat, met minder assemblage door functies te integreren en vaak ook een lager gewicht. We werken veel met bedrijven in de verpakkingsindustrie en in de automotive, dat zijn voor ons de hoofdmarkten. Qua producten moet je dan denken aan het 3D-printen van manifolds, grijpers, beugeltjes, klemmetjes, machineonderdelen en tandheugels. Een van onze klanten is Nedcar/BMW waarvoor we de tooling voor de Mini Countryman en de BMW X1 hebben ontworpen en 3D-geprint.
Een andere klant is Packland (Groot-Ammers). Daarvoor hebben we voor de productie van kitkokers de zogeheten overzetters gemaakt. Die overzetters zorgen dat kitkokers in dozen worden plaatst en vervolgens op een pallet worden gezet. Daarvoor hebben we gezamenlijk een herontwerp gemaakt. Voorheen was die overzetter een complexe samenstelling van onderdelen. De vacuümkoppen werden uit plaat gesneden, daarop werden de luchtkanalen gemonteerd met fittingen, zuignappen enz. enz. In totaal bestond die oude overzetter uit zo’n 200 onderdelen waarmee een monteur anderhalve dag bezig was deze te assembleren. Door het redesign konden we onder andere met hulp van de 3D-printer terug van 200 onderdelen naar 25 onderdelen. Dat bereikten we onder andere door de vacuümkanalen met de 3D-printer te integreren in de overzetter. Minder onderdelen betekent niet alleen minder assemblagetijd, maar ook nog eens een 80 procent lichter product. In plaats van 8 kg weegt de nieuwe overzetter nog maar 1,6 kg. En dat betekent weer dat de productielijn 15-20 procent sneller wordt omdat die meer plaatsingen per seconde kan doen.
SLS 3D-printer
SLS is de afkorting voor Selective Laser Sintering waarmee een product laag voor laag wordt opgebouwd waarbij gebruik wordt gemaakt van een poederbed. Een zogenaamde recoater legt een dun laagje poeder op het bouwplatform. Deze laag wordt verhit en een laser scant de doorsnede van het model. De laser versmelt zo het poeder en vormt een laag van het model. De recoater legt vervolgens een nieuwe laag poeder neer en het proces herhaalt zich totdat het geheel is opgebouwd. Het overgebleven poeder is na de bewerking opnieuw te gebruiken.