Eigenlijk wilde directeur Remi Castermans van Chromin in Maastricht de komende jaren langzaam maar gestaag groeien met zijn familiebedrijf. Een aanstaande grote opdracht in de automotive industrie gaat er echter naar verwachting voor zorgen dat de oppervlaktebewerker gespecialiseerd in diffusietechniek de komende jaren sneller gaat groeien dan ooit. Een verdubbeling van het aantal medewerkers ligt daarmee in het verschiet.
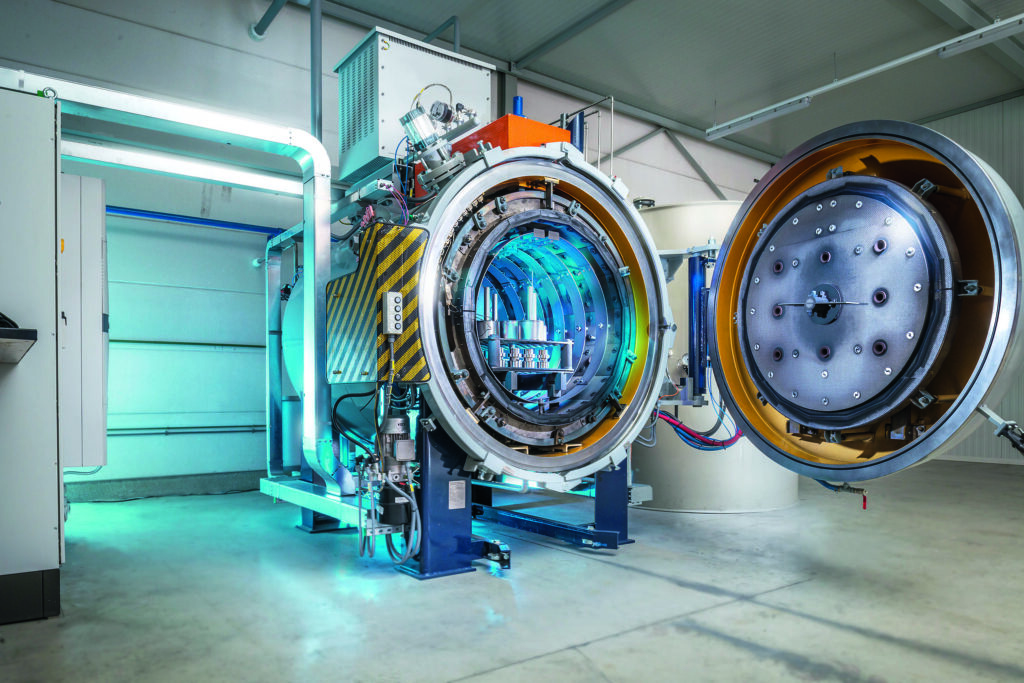
De opdracht levert het bedrijf voor zeven jaar werk op. ‘Ik ben positief ingesteld en ga er dus vanuit dat we die opdracht of een deel ervan binnen gaan halen. De automotive is nu al de grootste industrie waar we voor werken en dat gaat dus vanaf 2023 alleen nog maar toenemen. De huidige 22 mensen worden het vaste basisteam. We doen met ons allen dat nieuwe stukje bedrijf erbij waarbij de mensen meer verantwoordelijk worden voor de diverse afdelingen. We moeten dit grote project met zijn allen oppakken, anders lukt het niet. Alle neuzen moeten dezelfde kant opstaan.’
Om de nieuwe productie aan te kunnen, moet wel opnieuw een nieuwe hal worden gebouwd. Gelukkig had de voormalig directeur en vader van Castermans een vooruitziende blik en wist hij een paar jaar geleden grond van de buurman te kopen met nog wat omliggende percelen zodat straks 8500 vierkante meter bebouwd kan worden.
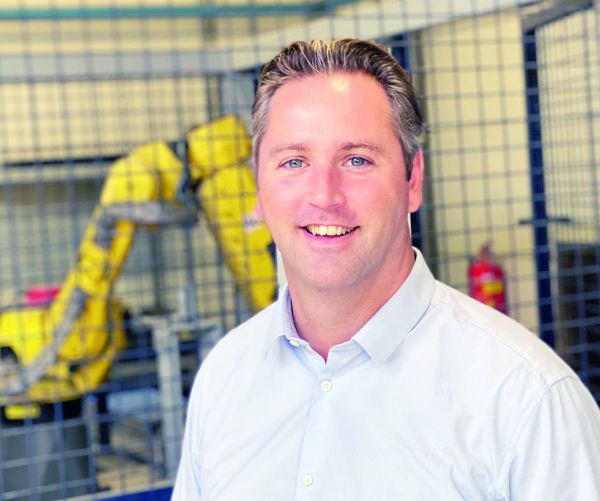
Procedé
In de hele wereld zijn volgens Castermans zover bekend vier bedrijven die met hetzelfde procedé werken als Chromin. In Nederland zijn alleen bedrijven die andere oppervlaktebehandelingen doen concurrent. ‘We verchromen niet, maar we brengen chroom in het materiaal. Daar komt ook onze bedrijfsnaam vandaan. Al onze processen zijn gebaseerd op de diffusietechniek, dat wil zeggen dat je op hoge temperatuur een element, in dit geval chroom, in het oppervlak brengt. Het doel is om een kwalitatief slecht materiaal wat makkelijk te bewerken is de eigenschappen te geven van een kwalitatief hoogstaand materiaal. Dat zorgt voor minder snelle slijtage en brengt de corrosiebestendigheid omhoog. Het is dus een laag in je materiaal in tegenstelling tot het verchromen.’
Diffusiecontainer
Voor het zogenoemde inchromeren gaan de materialen na binnenkomst in een hittebestendige diffusiecontainer. Hier worden de onderdelen met het chroompoeder ingezet. De container wordt afgesloten en gaat in een oven van, afhankelijk van het materiaal, met een temperatuur tussen de 850 en 1.000 graden. In een van de hallen staan 30 van deze diffusieovens. Onlangs werden drie nieuwe, aaneen te schakelen diffusieovens aangeschaft. Hierdoor kan Chromin producten tot een lengte van negen meter behandelen. ‘In de container vind een thermisch-chemisch proces plaats’, vertelt Remi. ‘Het chroom uit de poeder gaat heel graag een reactie aan met het koolstof in het materiaal. Zo ontstaat er chroomcarbide in het oppervlakte waarmee je een heel erg harde slijtvaste laag om het onderdeel sluit. Het chroom dringt in je materiaal, hierdoor ontstaat er een laagdiepte en geen opbouw wat een belangrijke voordeel geeft in de voedingsmiddelenindustrie.’
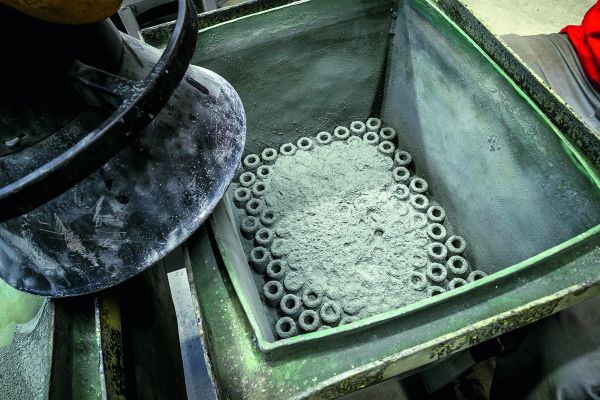
Vacuümoven
Om te kunnen inchromeren is het dus wel noodzakelijk dat er koolstof in het materiaal zit. In RVS bijvoorbeeld zit dat niet, maar Chromin kan het er op een speciale manier inbrengen. Dat gebeurde voorheen met zoutbaden van 900 graden, maar sinds een aantal jaren staat er bij Chromin een vacuümoven met een zelf ontwikkeld procedé. ‘In deze vacuümoven kunnen we het proces veel beter en preciezer regelen. Niet alleen de kwaliteit is omhoog gegaan, een ander belangrijk punt is dat we geen afvalzouten meer hebben. Dit proces is daarom veel minder slecht voor het milieu.’
Voedingsindustrie
Remi verwachtte dit jaar het beste jaar ooit te gaan draaien, maar de coronacrisis gooide roet in het eten. De omzet in de automotive daalde met zo’n veertig procent. Gelukkig is de voedingsindustrie een andere grote klant van Chromin. Daar wordt gewerkt met roestvast stalen materialen, die slijtagegevoelig zijn. De diffusietechniek van Chromin maakt het materiaal harder. ‘Hoewel we in de automotive door corona veel omzet zijn misgelopen, bleef het werk voor de voedingsindustrie goed doorlopen. De automotive verbetert nu wel weer, maar het zijn nog niet de aantallen van voor corona. Voor de crisis zaten op 120.000 onderdelen per maand. Ik verwacht nog wel een redelijk jaar, maar ik denk niet dat we het resultaat van vorig jaar gaan halen.’
De komst van de elektrische auto is een toekomstige uitdaging voor Chromin. ‘De lagen die wij inbrengen kunnen maximaal 850 graden verdragen, deze hoge temperatuurbestendigheid heb je bij een elektrische auto niet nodig. Daar komt nauwelijks tot geen warmte vrij. Daar zijn veel goedkopere oplossingen mogelijk.’
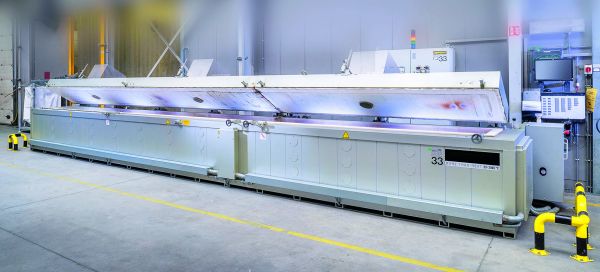
Loodvrij
Naast de automotive- en de voedingsindustrie werkt Chromin veel voor de soldeerindustrie. Hier wordt de techniek van Chromin gebruikt om de soldeermachines te beschermen. ‘In het verdrag van Kyoto is afgesproken dat alleen nog loodvrij gesoldeerd gaat worden. Bij het soldeer heb ze daarvoor loodvervangers gedaan. Maar deze waren op een bepaalde temperatuur zo agressief dat er gaten in de soldeermachines kwamen. Bij toeval zijn wij erachter gekomen dat onze laag daar bescherming voor biedt. Een alternatief was om de machines van titaan te maken, maar dat is onbetaalbaar. Omdat er steeds meer printplaten worden gemaakt waarvoor soldeermachines nodig zijn, verwachten we in deze business wel groei. Maar het zijn natuurlijk geen automotive aantallen.’
Bijblijven
Ook in de nabije toekomst wil Remi flink blijven investeren in het bedrijf. ‘We zijn natuurlijk al aan het automatiseren, met robots zijn we nu al aan het polijsten en in de toekomst willen we bijvoorbeeld ook met robots gaan inpakken. Ook wil ik het proces gaan door ontwikkelen. Daar hebben we de laatste jaren niet zo veel in geïnvesteerd. Het procedé is eigenlijk nog net zo als in 1977. Het principe met de container is gebleven. Er zijn enkele verbeteringen aan de receptuur doorgevoerd om de procestemperatuur omlaag te krijgen. Een andere grote stap was de aanschaf van de vacuümoven. Maar het inchromeren is en blijft een heel erg traag proces. Alles zit tussen de 15 en 30 uur in de oven. De meeste winst valt dus te behalen in de procesoptimalisatie hier omheen. Dat zijn de ideeën. Je wil niet stilstaan, we moeten bijblijven.’