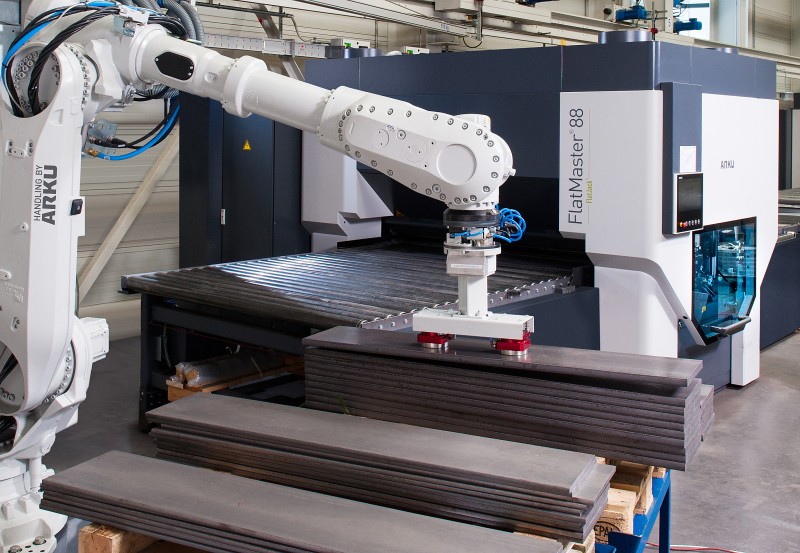
Arku Maschinenbau presenteerde tijdens zijn informatiedagen eind mei de nieuwste systemen voor het richten en ontbramen. Zo was er een live-demonstratie van de nieuwe FlatMaster 88 met vision-robot voor het automatisch laden en lossen van onderdelen en het FlatJack vlakheidcontrolesysteem.
Met de richtmachine, robot en kwaliteitscontrole kan de gebruiker autonoom plaat richten met een constant hoge kwaliteit. ‘We voeren de automatisering van onze machines verder op. Dit biedt onze klanten duidelijke voordelen’, legt Albert Reiss, managing partner bij Arku, uit. ‘Robotsystemen bieden zo een waardevolle ondersteuning – niet alleen in tijden van een tekort aan geschoold personeel – en garanderen zo betrouwbare werkprocessen.’
Om de voordelen van autonoom richten te leren kennen, konden bezoekers tijdens de informatiedagen zich vertrouwd maken met het volledige proces met hun eigen plaatwerkdelen. Dit tot een maximum gewicht van honderd kilogram. De werkwijze is als volgt. Als eerste worden de onderdelen in het werkgebied gepositioneerd en worden de materiaalspecificaties met behulp van een barcode ingelezen door de machine. Vanaf dan gaat alles automatisch. Camera’s scannen de onderdelen, die door het robotsysteem worden gedetecteerd, onafhankelijk van de hoogte, positie en positie van de stapel. De vision-robot selecteert, afhankelijk van het gewicht en de grootte, zelfstandig de onderdelen. De grijper legt de delen op de rollenbaan van de richtmachine, gevolgd door het richten van de plaat. De uitgelijnde plaatdelen worden gecontroleerd op vlakheid door het FlatJack controlesysteem. Na het rechtzetten pakt de vision-robot de onderdelen op en plaatst ze op een pallet.
Een onderdeel na het ontbramen en afschuinen met de EdgeBreaker 3000.
‘Op deze manier verhogen we de bezettingsgraad van de machines en ontlasten we de machinebedieners. Indien nodig kunnen we ook andere machinegroottes of voor onze ontbraamprocessen een autonome verwerking realiseren’, benadrukt Ewald Hund, hoofd ontwikkeling bij Arku.
Efficiënter ontbramen
De informatiedagen gingen niet alleen over het richten en de behandeling van plaatdelen. Arku maakte ook gebruik van deze gelegenheid om zijn assortiment ontbraammachines te presenteren.
Zo is er de nieuwe EdgeBreaker 3000 ontbraammachine voor laseronderdelen. ‘Deze ontbraammachine heeft twee in serie geschakelde bewerkingszones, die aan beide zijden in één bewerking de plaatdelen tot een dikte van 80 mm kunnen ontbramen en afronden. Door in één arbeidsgang te ontbramen én af te ronden, bespaart dit ongeveer de helft van de bewerkingstijd. Zelfs grote hoeveelheden kunnen zo tijdbesparend verwerkt worden. De stukskosten liggen daarmee duidelijk een stuk lager dan andere processen of handmatige verwerking’, legt Hund uit.
De EdgeBreaker 3000 biedt volgens Arku nog meer voordelen dankzij het gepatenteerde borstelwisselsysteem. Dit maakt een eenvoudige en snelle vervanging van de slijpmiddelen en dus een snelle en flexibele aanpassing aan de ontbraamwerkzaamheden mogelijk. De automatische kalibratie meet ook het verbruik van het schuurmiddel en compenseert dit automatisch. De exploitant hoeft niet verder in te grijpen.
Procesgegevens in oogopslag
Naast de machines presenteerde Arku samen met partner Axoom ook een digitale oplossing voor het verzamelen en weergeven van procesdata. Het bedrijf presenteert een web-based interface waarmee machinegegevens zoals machineconditie, capaciteitsbenutting of energie-efficiëntie vanaf elke locatie kunnen worden gecontroleerd. ‘Onze klanten willen altijd op de hoogte blijven. Wij bieden hen de juiste oplossing’, beweert Hund.
Geëvalueerd
Zo kan de productiemanager in één oogopslag zien welke installaties in bedrijf zijn en waar vrije capaciteit beschikbaar is. Ook de productiviteit en het energieverbruik kunnen zo worden geëvalueerd. ‘Met de gebruikersinterface hebben klanten volledige transparantie over de voor hen belangrijke machinegegevens en kunnen ze snel reageren op eventuele afwijkingen. Dit werkt positief voor de efficiëntie van plaatbewerking.’